If you’ve ever wondered how plasma — that glowing, charged gas — is actually made in a lab or industrial setting, you’re not alone. Sure, it looks like something straight out of science fiction, but in reality, plasma is produced every day in cleanrooms, fabrication plants, and even hospitals. And the magic behind it? It all comes down to three key pieces of equipment: an RF Generator, a Matcher, and an RPS, or Remote Plasma Source. Let’s walk through the whole process in plain English, from start to spark.
What Exactly Is Plasma?
Let’s get this out of the way first. It isn’t just “hot gas.” It’s actually the fourth state of matter — think solid, liquid, gas… and then plasma. It’s made up of free electrons and ions, and it conducts electricity. You’ll find it in neon signs, lightning bolts, and, more importantly for us, in semiconductor processing. It’s used to etch materials, clean surfaces, and treat wafers in ways nothing else can.
What Do You Need to Make It?
Creating plasma isn’t as simple as flipping a switch. You need a vacuum environment, a gas to ionize (like argon or oxygen), and most importantly, energy — typically in the form of high-frequency RF power. That’s where our trio comes in: the RF Generator, the Matcher, and the RPS.
The RF Generator – Where the Power Begins
Think of the RF Generator as the power plant. It generates high-frequency electrical energy, usually at standardized frequencies like 13.56 MHz or 27.12 MHz. These aren’t random numbers — they’re internationally approved ISM (Industrial, Scientific, Medical) bands.
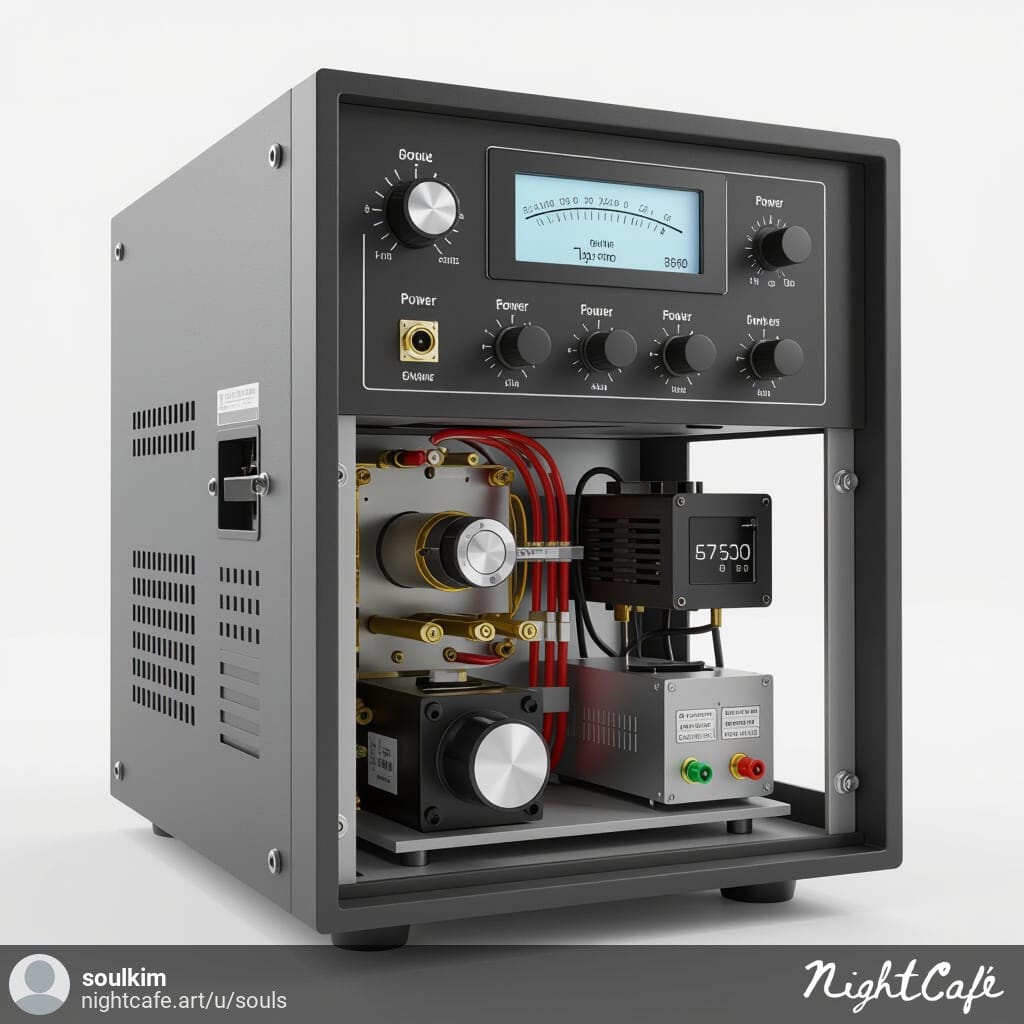
The RF Generator’s job is simple: supply stable, clean RF power. But — and this is important — that power alone isn’t enough to create plasma. You can’t just dump it into a chamber and expect results. That’s where the Matcher comes in.
The Matcher – Bridging the Power Gap
Here’s where it gets interesting. The Matcher (often called a matching network or impedance matcher) makes sure that the power from the RF Generator actually makes it to the plasma chamber — without getting reflected back. Why would it reflect? Because the impedance of the plasma (which constantly changes!) usually doesn’t match the output impedance of the generator.
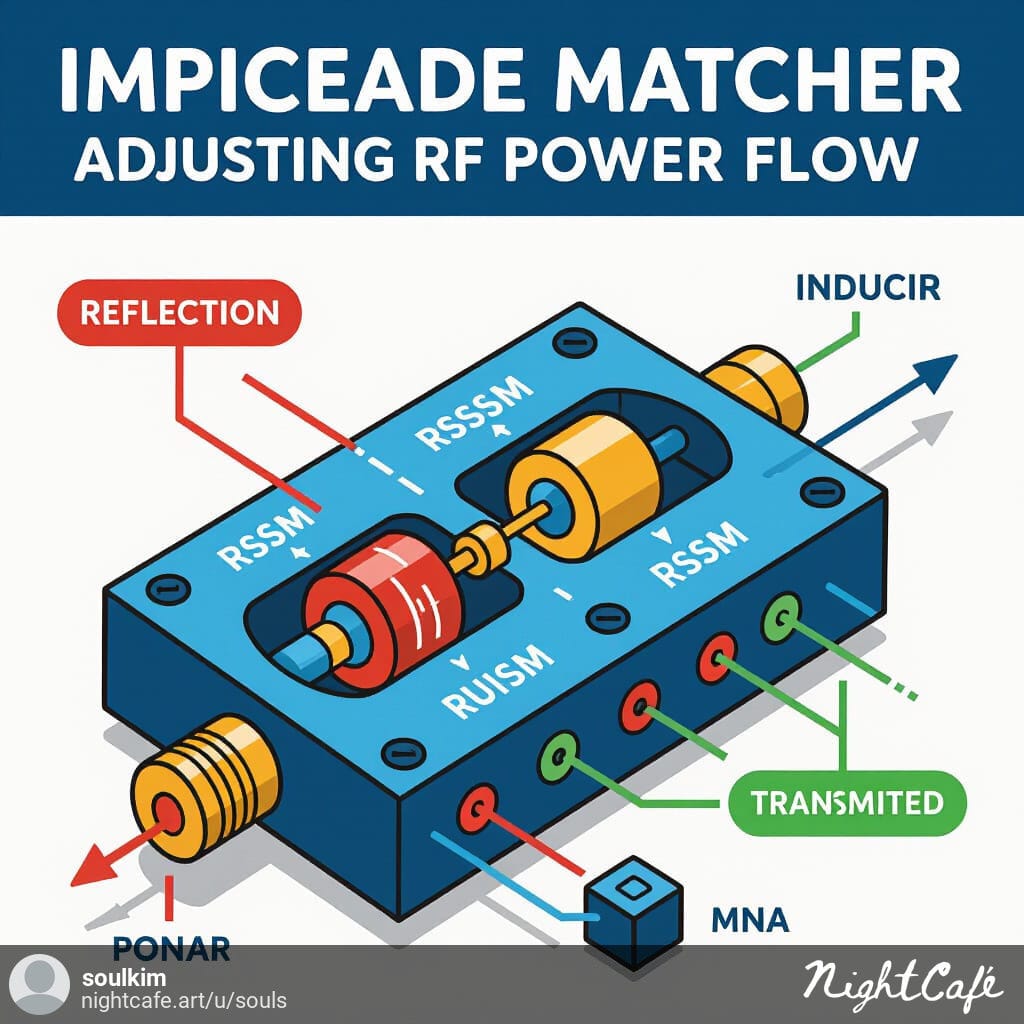
Imagine trying to pour water into a hose that’s half-blocked — not much is getting through. The Matcher fixes that by adjusting capacitors and inductors in real time to “match” the load. That way, energy flows smoothly from the source to the destination, without bouncing back and frying your equipment.
The RPS – Where the Magic Happens
Now, the Remote Plasma Source (RPS) is where the actual plasma is formed. The RPS takes the tuned RF power and delivers it into a gas-filled chamber. The high-frequency energy strips electrons from the gas atoms, creating ions and free electrons — boom, plasma!
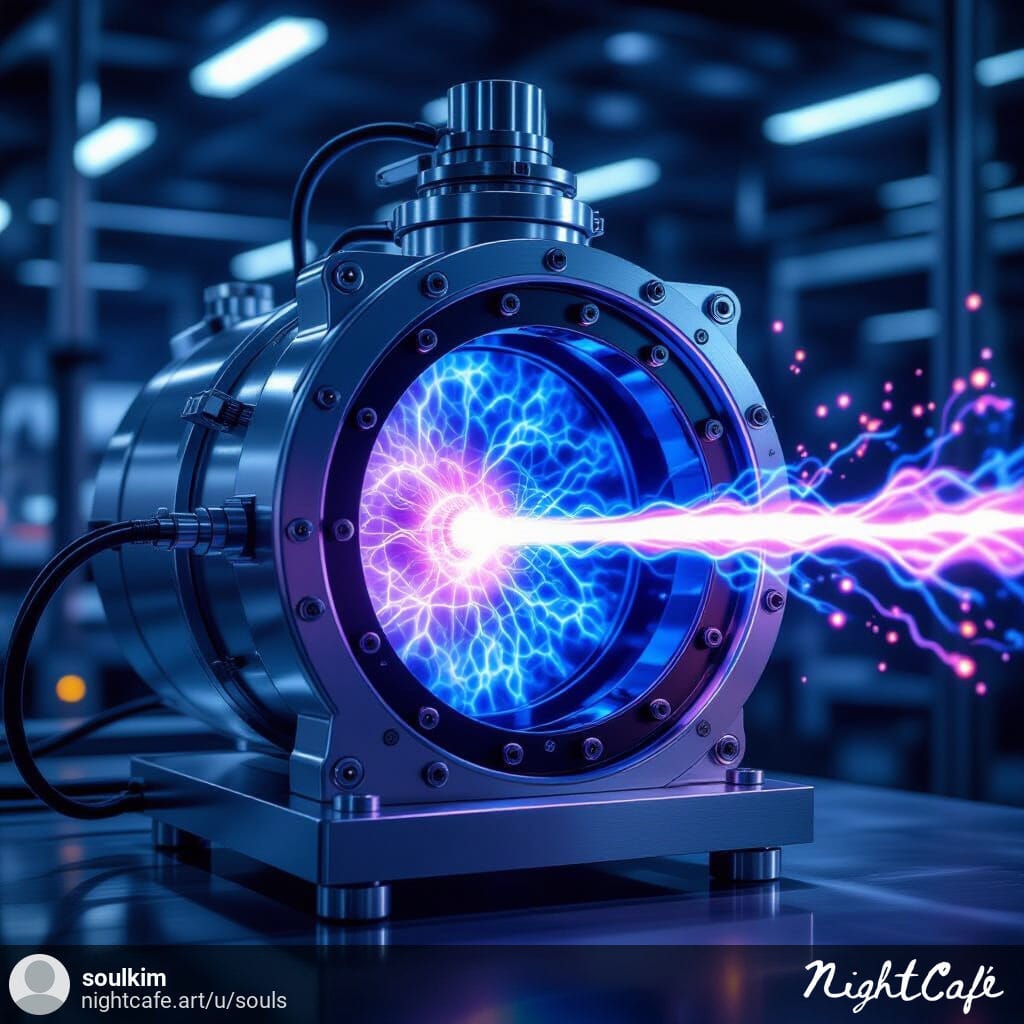
What’s cool about the RPS is that it’s usually separated from the main process chamber, hence “remote.” This isolation makes it easier to control and helps keep the plasma stable, clean, and tailored to the process.
From Generator to Plasma – How It All Flows
So how do these three work together? Here’s a simplified flow:
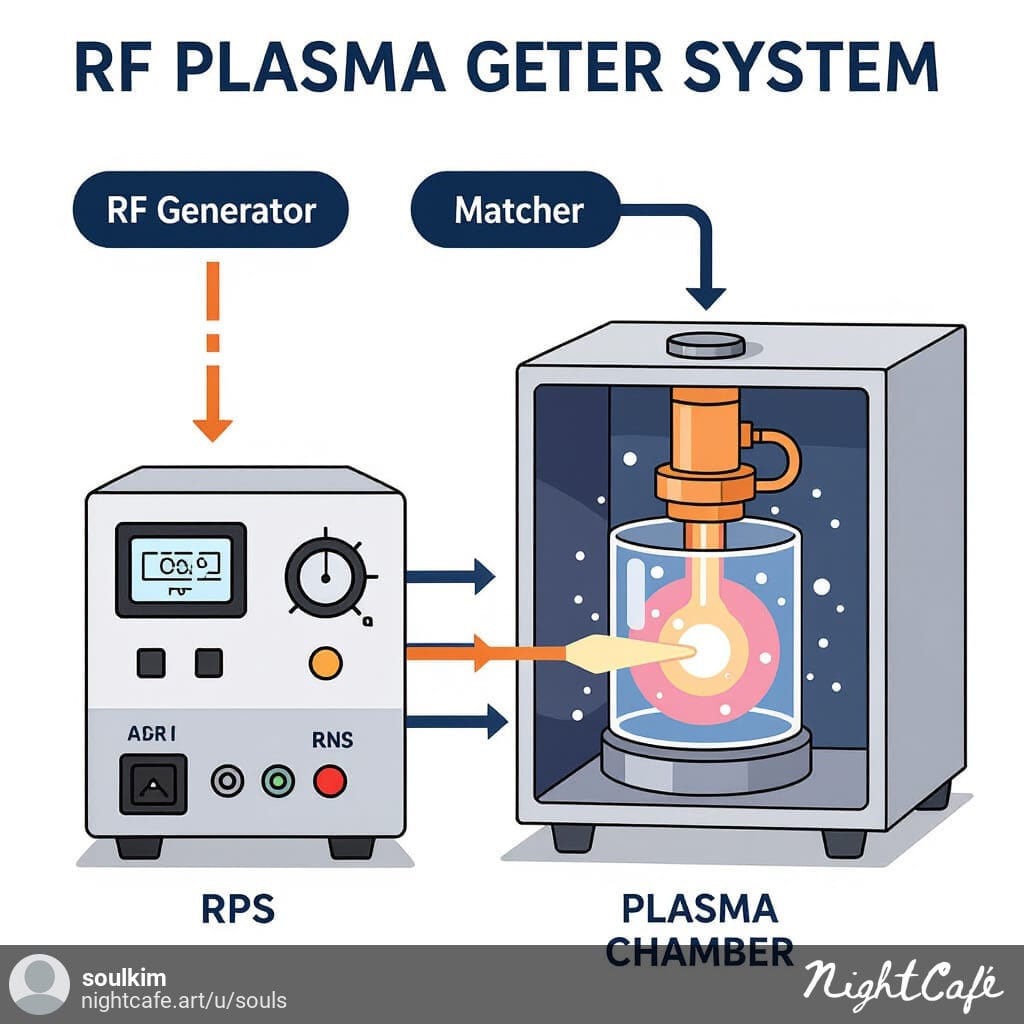
[RF Generator] → [Matcher] → [RPS] → Plasma is generated
- The RF Generator produces the energy.
- The Matcher adjusts impedance to make sure there’s no power loss.
- The RPS receives this optimized power and turns it into plasma.
It’s a synchronized dance of electronics, magnetics, and gases — and if even one part is off, plasma either won’t form at all or will be unstable.
A Simple Flow Chart of the Plasma Generation Process
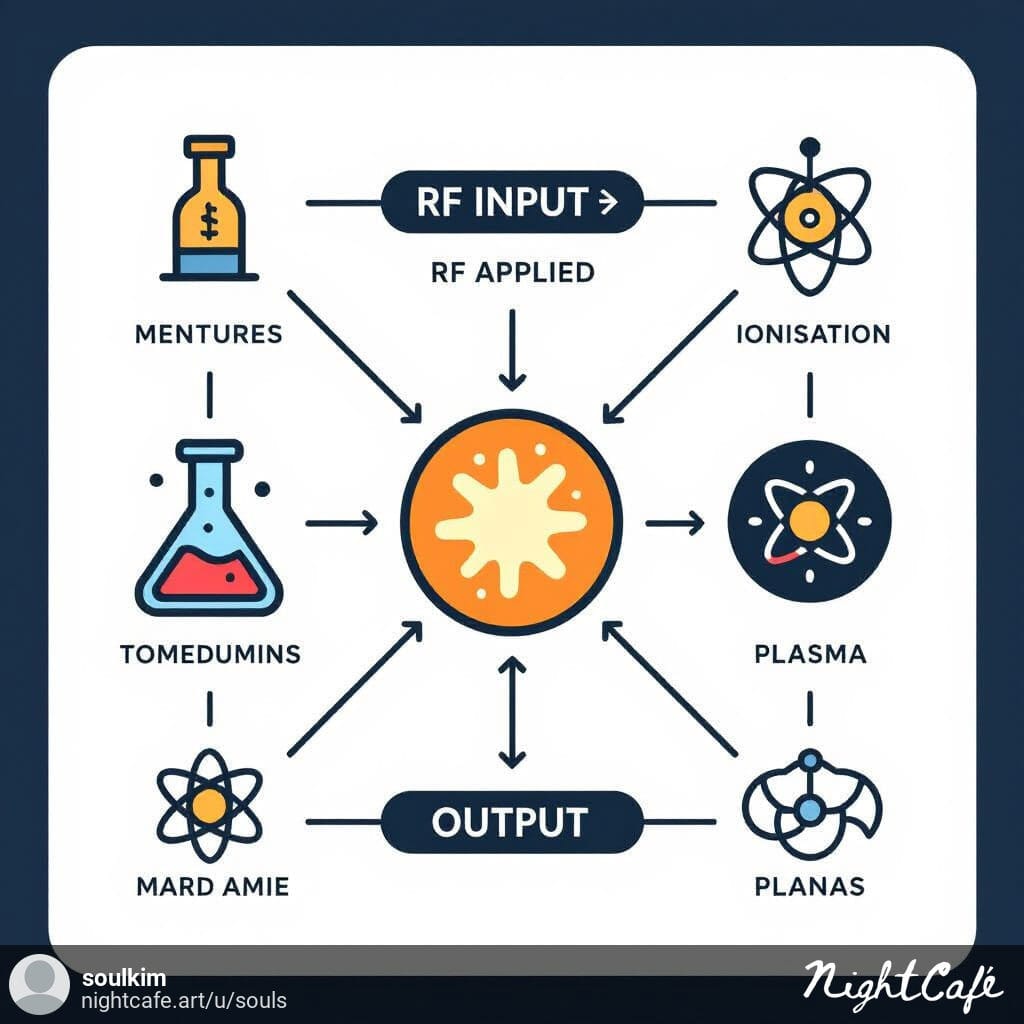
If you’re more of a visual person, picture this:
Gas Inlet → RPS Chamber → RF Energy Applied → Electrons Excited → Ionization → Plasma Formed → Process Gas Out
This is happening at incredible speeds, often under vacuum, with precise gas flow rates and tight temperature controls. It’s engineering at its finest.
What Happens After Plasma Is Formed?
Once plasma is up and running, it gets directed to wherever it’s needed — usually into a processing chamber. There, it’s used to etch patterns into wafers, clean residues from surfaces, or activate chemical reactions. Because plasma is so reactive, it can do things that regular heat or chemicals can’t — all while staying incredibly precise.
Real-World Applications
This RF-plasma setup isn’t just theory. It’s at the heart of real-world industries like:
- Semiconductor fabrication (etching, stripping, cleaning)
- Flat-panel display manufacturing
- Medical device sterilization
- Thin-film deposition and surface treatment
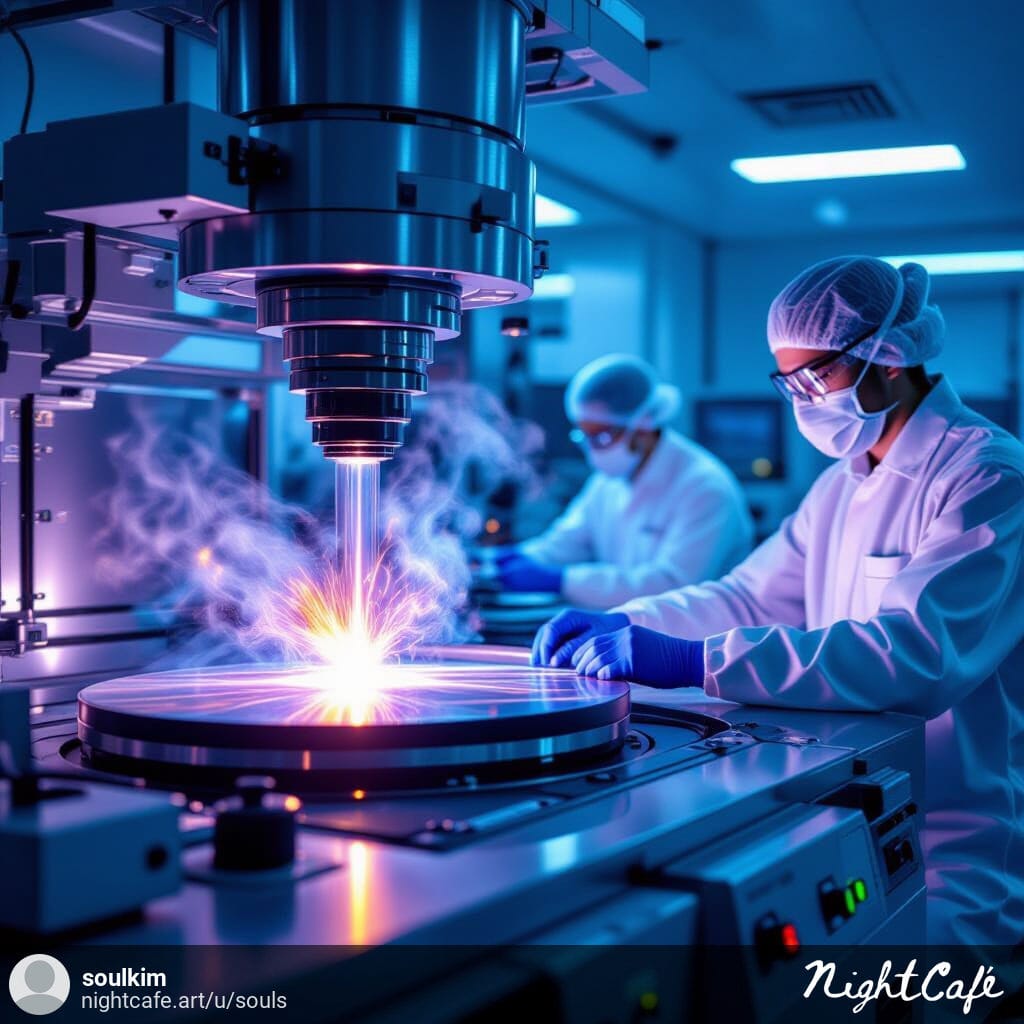
Any time you need controlled, powerful surface interaction at the atomic level, plasma is your best friend.
Things to Keep in Mind
Now, not all systems are the same. Depending on your application, you’ll want to consider:
- Power levels: Are you working with 200W or 5kW?
- Gas types: Different gases produce different plasmas.
- Process stability: Fluctuating loads may require automatic matchers.
- Control systems: Do you need analog, digital, or remote control?
And don’t forget: plasma can be hard on equipment. Maintenance matters. Keep those matchers calibrated and check for reflected power regularly.
Looking Ahead – Where Is Plasma Tech Going?
The future is smart. Matchers are getting automated, RF Generators are getting digital feedback loops, and RPS units are becoming smarter with built-in sensors and AI tuning. We’re heading toward fully closed-loop plasma control systems — less guesswork, more precision, and better yields.
Wrapping It Up
So, how do you make plasma? You bring together an RF Generator to produce the energy, a Matcher to make sure none of that energy is wasted, and an RPS to finally ignite the plasma. It’s not magic — it’s physics, engineering, and precision working in harmony.
Whether you’re working in a lab, a fab, or just learning the ropes, understanding this trio is essential. Plasma doesn’t just happen — we make it happen, one tuned signal at a time.
What Is the Matcher? Essential RF Matcher Guide Made Simple
Leave a Reply