1. Introduction
In semiconductor manufacturing and advanced materials processing, precision, purity, and control are critical. Remote Plasma Source (RPS) technology provides a reliable solution for plasma-based cleaning and reactive gas generation, offering engineers a clean and efficient way to manage complex process environments.
2. What Is RPS?
Remote Plasma Source (RPS) is a device used to generate reactive plasma species outside the main process chamber. Unlike in-situ plasma, which is generated directly within the chamber, RPS isolates the plasma generation, reducing contamination and minimizing damage to sensitive wafers or components.
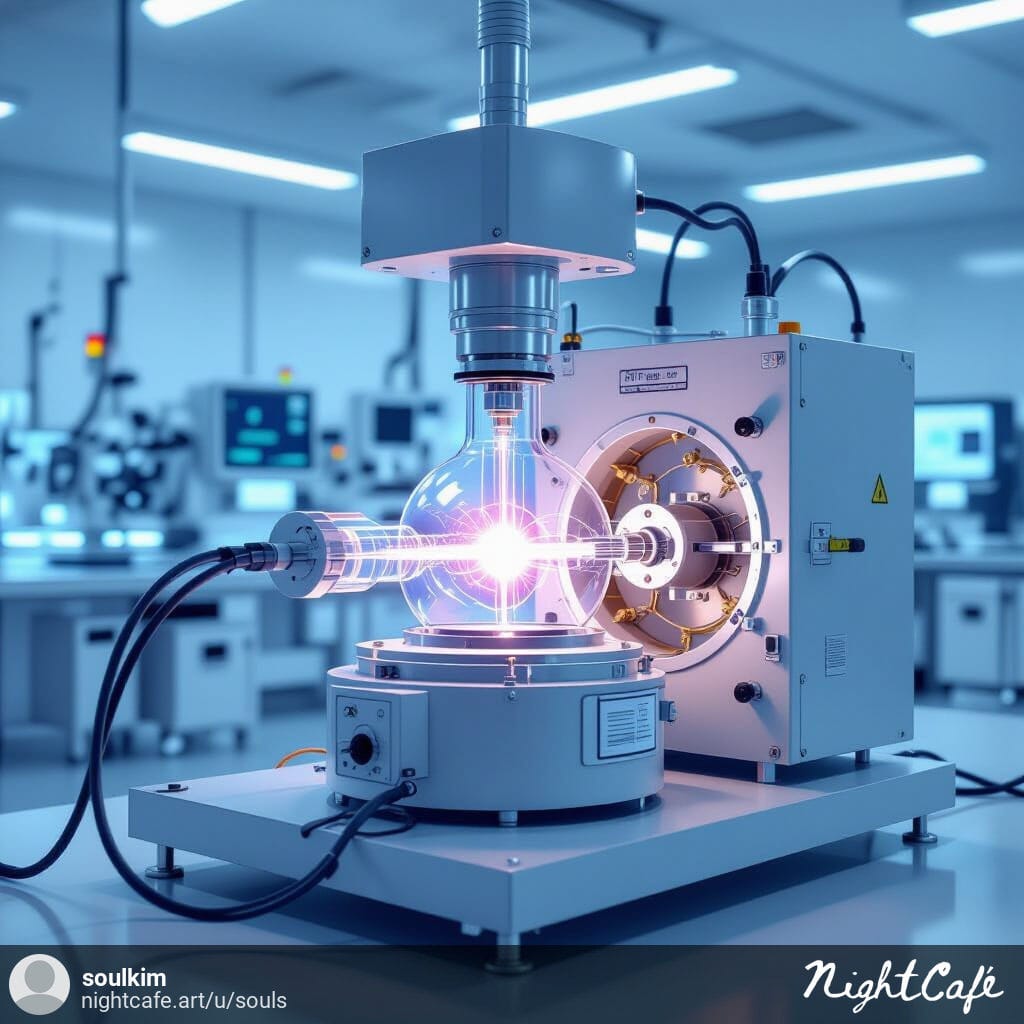
3. How RPS Works
RPS units typically use gases like NF₃, O₂, or H₂ mixed with carrier gases such as Ar or He. These gases are introduced into the plasma chamber, where high-frequency RF or microwave power ionizes them, forming reactive radicals (e.g., fluorine atoms, oxygen radicals). The reactive species are then transported downstream into the process chamber via a delivery line, enabling plasma-based reactions without direct plasma exposure.
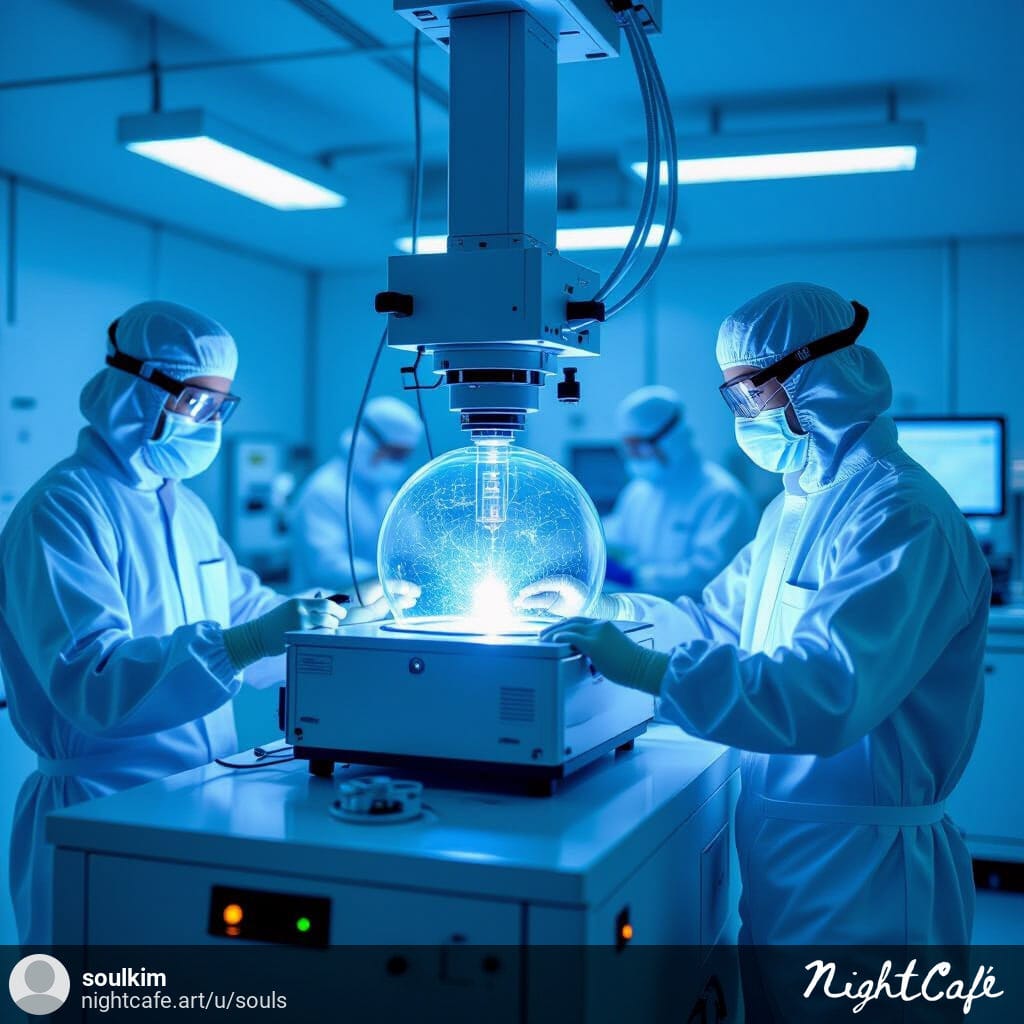
4. Where RPS Is Used
RPS systems are widely used in:
- Semiconductor wafer cleaning (ash/removal of photoresist or residues)
- Chamber cleaning (especially CVD, ALD, and PECVD systems)
- Display panel fabrication (OLED/LCD)
- Etching processes requiring minimal plasma damage
- Surface activation and pre-treatment in advanced packaging
5. Why RPS Matters
The primary advantage of RPS lies in its remote generation of plasma, which leads to:
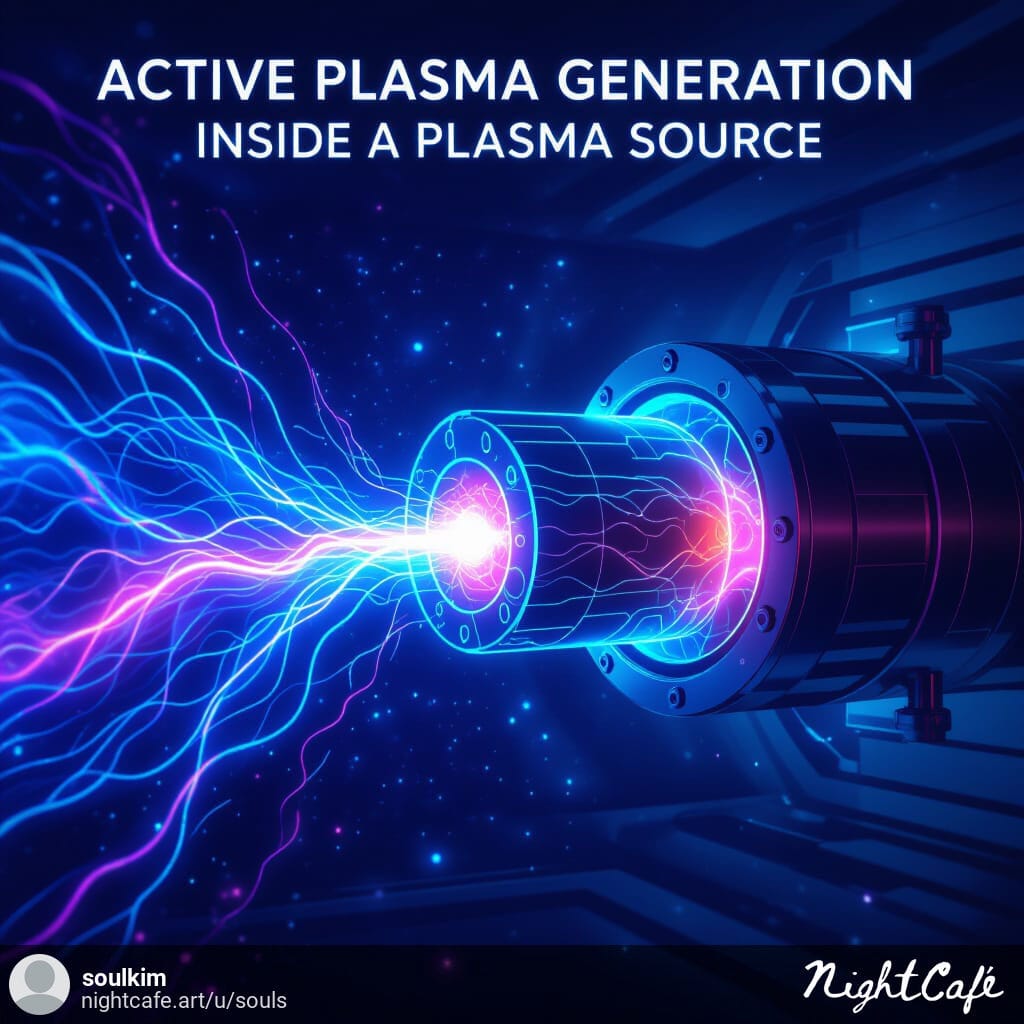
- Reduced particle contamination
- Lower ion damage to substrates
- Better chamber lifetime and reduced maintenance
- Improved control of radical species density
These features are essential in modern high-precision manufacturing, especially at sub-10nm process nodes.
6. Key Features of RPS
- Microwave or RF-based plasma generation
- Gas compatibility (NF₃, O₂, H₂, Cl₂ depending on process)
- Real-time plasma monitoring (with optical emission sensors)
- Thermal management (cooling systems to handle heat)
- Plasma-on-demand with controlled ignition timing
7. Common Failure Modes
Despite its robustness, RPS systems can experience various issues:
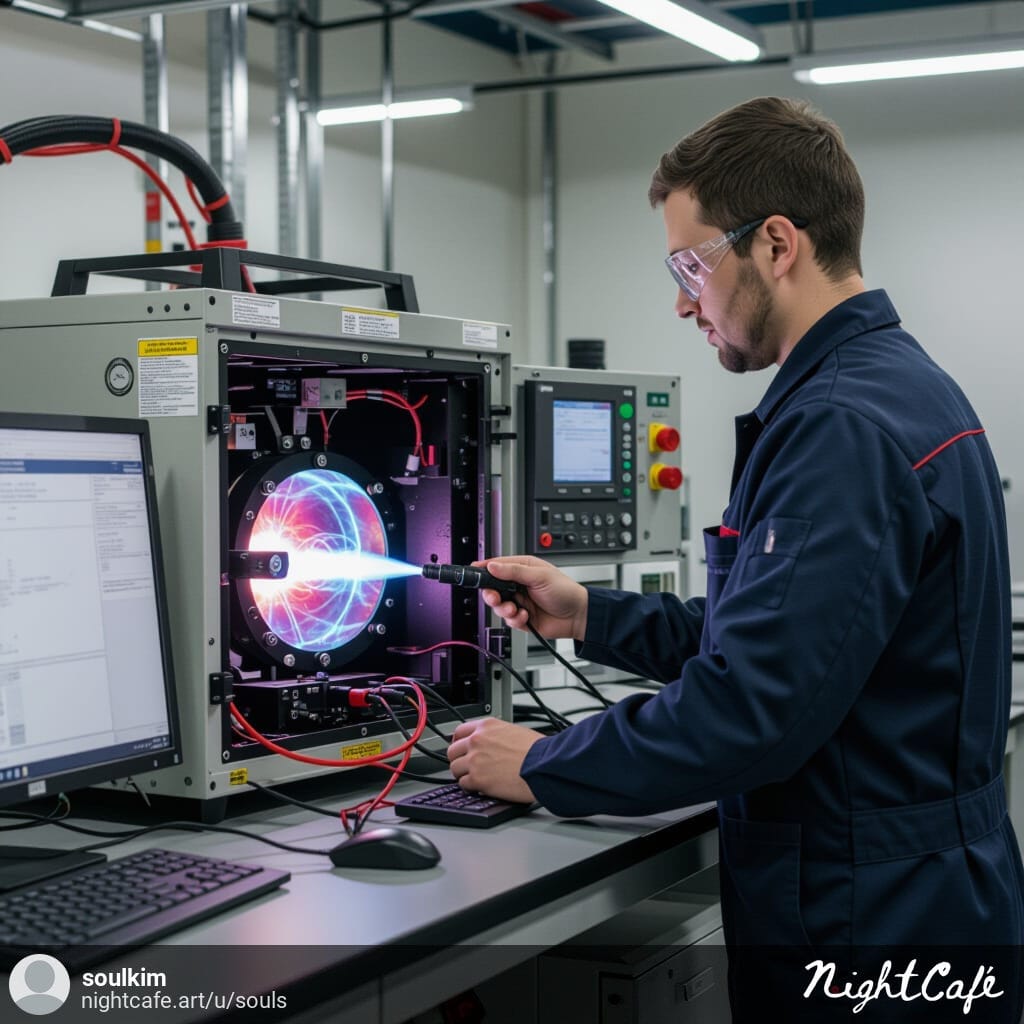
- Ignition Failure: Caused by degraded RF components or gas flow issues
- Arcing and Discharge Instability: Often due to pressure variations or faulty matching networks
- Plasma Source Degradation: Over time, electrodes or quartz components degrade under high energy
- Gas Delivery Issues: Blocked lines or mass flow controller (MFC) errors can disrupt gas ratios
- Cooling Failure: Insufficient thermal dissipation can cause overheating and shutdowns
8. Maintenance and Troubleshooting
Effective RPS maintenance includes:
- Regular electrode and quartz tube replacement
- RF power monitoring and impedance matching checks
- Scheduled gas line purging
- Cooling system inspection (pumps, chillers, flow rates)
- Plasma emission analysis to detect abnormal behavior
Advanced systems also integrate self-diagnostics and error logging for predictive maintenance.
9. Future Trends in RPS
As semiconductor processes evolve, so does the need for more efficient and compact RPS units. Trends include:
- Integration with AI-based process control
- Miniaturized plasma sources for ALD/3D NAND applications
- Higher energy efficiency through solid-state RF technology
- Advanced plasma chemistry modeling and simulation tools
10. Personal Insight
In high-volume manufacturing fabs, I’ve seen RPS units act as unsung heroes—rarely at the center of attention, but critical to uptime, yield, and contamination control. What impresses me most is how such a compact unit manages to deliver high-purity plasma chemistry with minimal disturbance to the main chamber. Engineers who truly understand RPS functionality often hold the key to process optimization and downtime reduction.
Leave a Reply